Unleash the Potential with NEC Contracts: A Comprehensive Guide to Strategic Project Management
NEC contracts have become a popular choice for construction projects worldwide, offering a framework built on collaboration and cooperation. These contracts provide a structured approach to project management while encouraging all parties to work together toward common goals. NEC contracts are suitable for a wide range of works, services and supplies, delivering significant time and cost savings while enhancing quality outcomes.
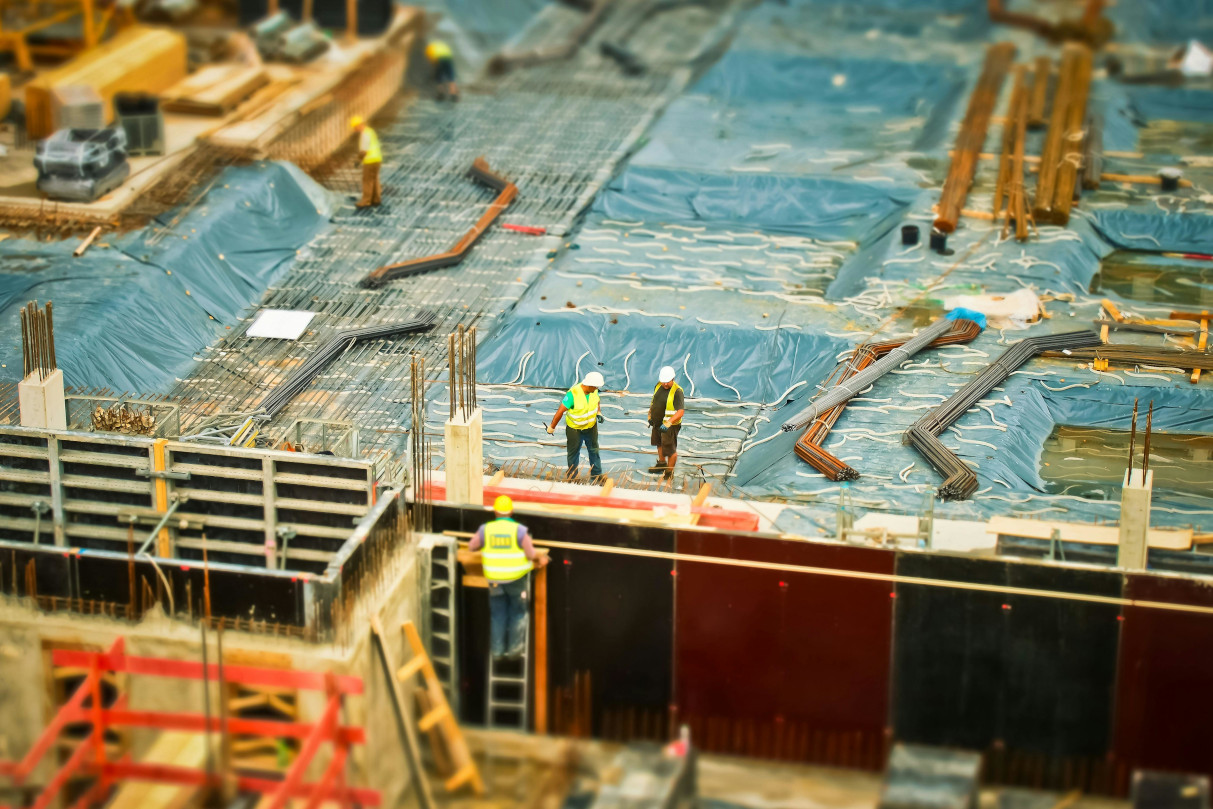
The NEC suite stands out from traditional construction contracts because of its focus on mutual trust and cooperation. This approach helps reduce disputes and creates a more positive working environment for all involved. Project teams using NEC contracts often find they can resolve issues more quickly and maintain better working relationships throughout the project lifecycle.
Many organisations are still not using NEC contracts to their full potential. By understanding the core principles behind these contracts and implementing them correctly, project teams can streamline processes, improve communication and achieve better results. The flexible nature of NEC contracts makes them adaptable to various project types, providing the structure needed while allowing for creativity in finding solutions.
Understanding NEC Contracts and Their Fundamentals
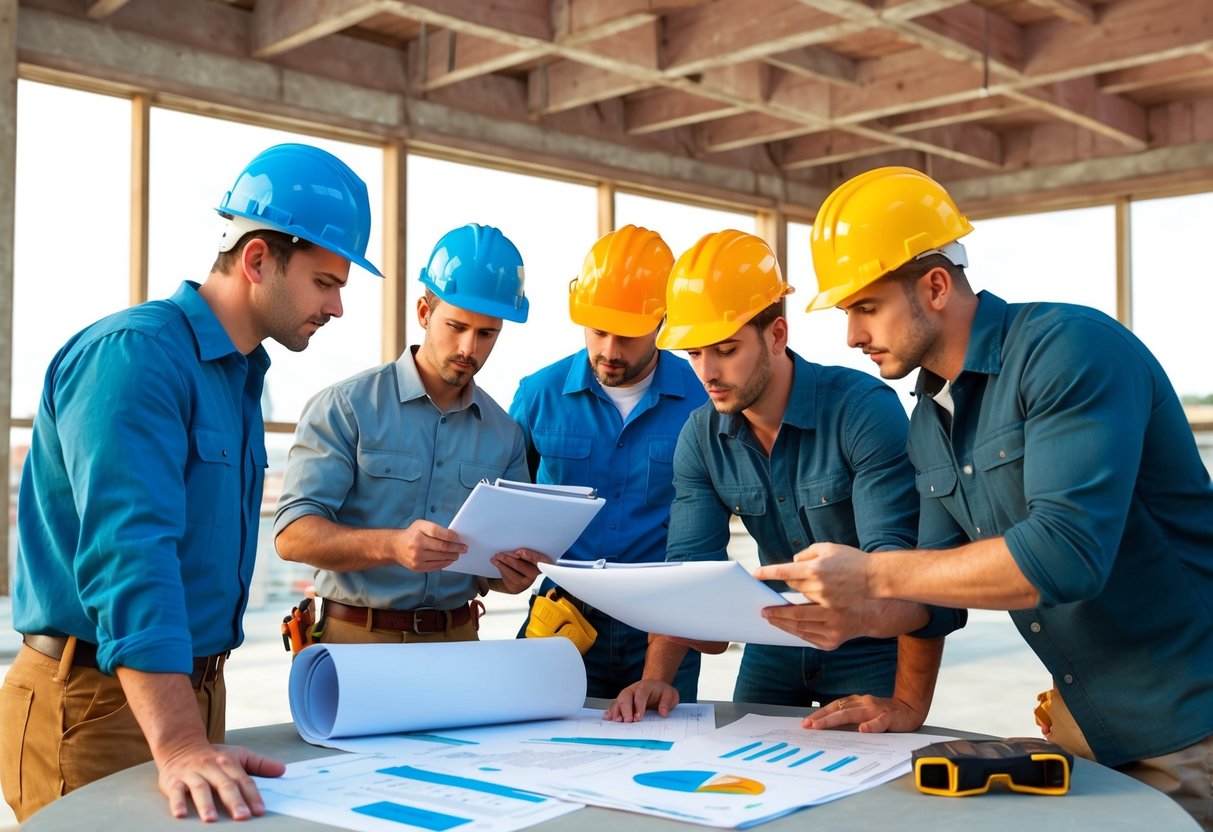
NEC contracts offer a unique approach to project management that emphasises collaboration and clarity. These contracts have transformed how construction and engineering projects are managed across the UK and internationally.
Overview of NEC and NEC4
NEC stands for New Engineering Contract, a family of contracts designed to improve project delivery. NEC4, the latest version, builds on previous iterations with enhanced features for modern construction needs.
NEC contracts were developed by the Institution of Civil Engineers to address traditional contractual problems in the industry. They are known for their plain English approach, making them accessible to all project participants.
The NEC suite includes various contract types:
- Engineering and Construction Contract (ECC)
- Professional Service Contract (PSC)
- Term Service Contract (TSC)
- Supply Contract (SC)
Each contract type serves different project requirements, making the NEC system highly adaptable across sectors. NEC4 specifically includes improved provisions for collaboration, dispute avoidance, and BIM integration.
General Principles and Structure of NEC4 Contract
NEC4 follows core principles that set it apart from other contract forms like FIDIC. The most fundamental principle is the requirement for parties to act “in a spirit of mutual trust and co-operation.”
The structure of NEC4 is modular and includes:
- Core clauses (applicable to all options)
- Main option clauses (payment mechanisms)
- Secondary option clauses (additional provisions)
- Contract data (project-specific information)
This modular approach allows for flexibility whilst maintaining consistency. The contract emphasises proactive risk management through early warning procedures and regular programme updates.
NEC4 contracts use simple present tense and avoid legal jargon. This clarity helps reduce misunderstandings between the client and contractor. Guidance notes accompany the contracts to assist users in implementation.
Roles and Responsibilities in NEC Contracts
NEC contracts define key roles with specific responsibilities for effective project delivery. The primary roles include:
The Client/Employer: Provides requirements, makes payments, and appoints key team members. They must respond promptly to communications and maintain overall project oversight.
The Contractor: Responsible for delivering works according to the scope and programme. They must give early warnings of potential issues and submit regular programme updates.
The Project Manager: Acts as the client’s representative, assessing progress, certifying payments, and managing changes. Their decisions directly impact the contractor’s time and cost.
The Supervisor: Monitors quality and compliance with the scope. They have authority to inspect work and reject non-compliant items.
Communication between these parties follows structured formats with specified response times. This clarity in roles minimises conflicts and ensures smoother project delivery.
Strategic Considerations for Successful NEC Contract Management
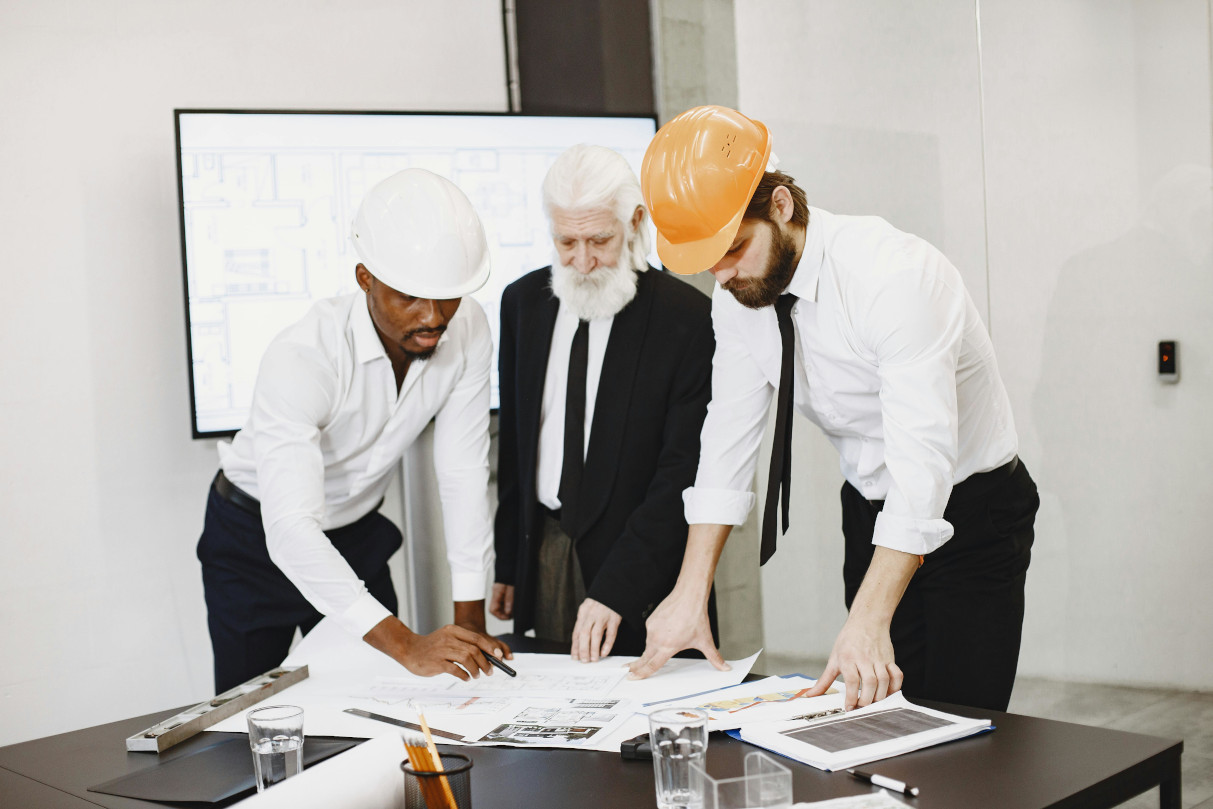
Managing NEC contracts effectively requires strategic planning and a clear understanding of the unique framework they provide. Success hinges on establishing proper collaborative relationships, implementing robust risk management processes, and selecting appropriate procurement strategies.
Collaborative Approach and Trust
NEC contracts are designed to foster collaboration between all parties. This collaborative approach is not merely suggested but contractually required through clauses that mandate regular communication and cooperative problem-solving.
Trust forms the foundation of this collaboration. Parties must operate with transparency, sharing information openly to identify and resolve issues promptly. The contract administrator plays a crucial role in maintaining this trust by providing fair assessments and timely responses.
Regular progress meetings help establish a positive working environment. These meetings should focus on solutions rather than blame, encouraging all participants to contribute constructively to the project’s success.
Training team members specifically in NEC procedures ensures everyone understands their obligations. This shared knowledge creates a common language for discussing contract matters and reduces misunderstandings that might damage trust.
Risk Allocation and Management
NEC contracts feature sophisticated risk management mechanisms that require active participation from all parties. Early warning provisions compel stakeholders to identify potential issues before they impact the project.
Risk registers should be maintained and regularly reviewed. These documents track identified risks, their potential impact, and mitigation strategies. They should be living documents that evolve throughout the project lifecycle.
Clear allocation of risks between parties prevents disputes. The contract should explicitly state who bears responsibility for specific risk categories, with consideration given to which party can best manage each risk.
Insurance requirements and performance bonds must align with the risk profile. These financial safeguards protect all parties but should be proportionate to potential liabilities to avoid unnecessary costs.
Safety risks demand particular attention in construction projects. The contract should establish robust safety protocols and reporting systems to prevent accidents and ensure compliance with regulations.
Procurement Strategies and Best Practices
Selecting the appropriate NEC contract option forms the cornerstone of effective procurement. Each option (A through F) offers different payment mechanisms and risk allocations to suit various project types.
NEC Contract Options at a Glance:
Option | Description | Best Suited For |
---|---|---|
A | Priced contract with activity schedule | Well-defined projects with clear scope |
B | Priced contract with bill of quantities | Projects with quantifiable work items |
C | Target contract with activity schedule | Complex projects with shared risk |
D | Target contract with bill of quantities | Complex projects with quantifiable work |
E | Cost reimbursable contract | Highly uncertain or emergency work |
F | Management contract | Projects requiring contractor expertise |
Early contractor involvement often delivers significant value. Bringing contractors into the planning phase helps identify buildability issues and opportunities for innovation before designs are finalised.
Market testing ensures competitive pricing while maintaining quality standards. Multiple-stage procurement processes can evaluate quality and capability before price considerations.
Value engineering workshops encourage all parties to identify cost-saving opportunities without compromising project outcomes. These collaborative sessions exemplify the best practice approach that NEC contracts are designed to support.
Critical Aspects of NEC Contract Execution
NEC contracts require attention to specific actions and responsibilities to achieve project success. Understanding how to handle defects, manage documentation, and comply with safety regulations can significantly impact project outcomes.
Handling Defects and Liability
Defects management under NEC contracts follows a structured approach that differs from traditional contracts. When a defect is identified, it must be notified promptly to the contractor who is then obliged to rectify it within the defect correction period.
The contract clearly defines what constitutes a defect – any work that doesn’t meet the requirements stated in the Works Information. This includes both visible and latent defects that may appear after completion.
Liability for defects extends beyond practical completion. The defects liability period (often 12 months) allows the client to identify issues that weren’t apparent at handover.
Retention monies are typically held as security against defects. The retention fund (usually 3-5% of contract value) is released in two stages – half at completion and half after the defects liability period ends.
Insurance requirements must be carefully followed to ensure coverage for defects and potential claims. NEC contracts are specific about minimum coverage levels and duration.
Managing Project Documentation and Communication
NEC contracts demand robust documentation practices and open communication between all parties. Early warning notices are a cornerstone of the NEC approach, requiring proactive identification of potential issues.
Programme updates must be submitted regularly, showing actual progress against planned timelines. These become crucial records if disputes arise about delay damages or extensions of time.
Project communications must follow the formal channels specified in the contract. This typically means using standardised forms and following prescribed notification periods.
Records of all instructions, variations and compensation events need meticulous maintenance. Each communication becomes a contractual document that may be referenced later if disagreements occur.
Digital documentation systems can help manage the volume of paperwork. Many construction projects now use dedicated software to track NEC-specific documentation requirements.
Ensuring Compliance with Safety and Legislation
Safety standards are non-negotiable in NEC contracts. The contractor must comply with all relevant health and safety legislation and often needs to produce specific plans and risk assessments.
Regular safety audits should be conducted, with findings documented and acted upon. The contract will specify who is responsible for these audits – typically either the Project Manager or a designated safety consultant.
CDM (Construction Design and Management) Regulations must be followed rigorously. These assign specific duties to clients, designers, and contractors regarding safety throughout the project lifecycle.
When partial possession occurs, safety responsibilities must be clearly delineated. This includes defining access rights, ongoing works permissions, and liability boundaries.
Surveyors play a crucial role in verifying compliance with building regulations and planning conditions. Their reports form part of the essential documentation trail required by NEC contracts.
Advanced Application of NEC Contracts in Construction Projects
NEC contracts offer sophisticated applications for complex construction projects. Their flexible structure allows integration with modern practices while maintaining clear responsibilities between contractors, subcontractors, and project managers.
Incorporating Building Information Modelling (BIM) and Sustainability
NEC4 contracts specifically address BIM integration through information modelling provisions. These clauses establish clear protocols for data exchange and model ownership throughout the project lifecycle.
The contracts support sustainability through works information requirements. Contractors can be contractually bound to specific environmental targets, waste reduction protocols, and social value commitments.
For infrastructure projects, NEC forms incorporate sustainability metrics directly into performance indicators. This approach links payment mechanisms to sustainable outcomes.
Key sustainability elements in NEC contracts:
- Carbon reduction targets
- Waste management protocols
- Community benefit requirements
- Resource efficiency standards
Facilities management considerations can be embedded within the term service contract variations, ensuring long-term sustainability beyond construction.
Facilitating Sectional and Partial Completion
NEC contracts excel at managing complex phased deliveries through sectional completion provisions. This approach allows clients to take possession of completed portions while work continues elsewhere.
The contract clearly defines:
- Specific completion dates for each section
- Separate defects notification periods
- Proportional release of retention funds
- Sectional delay damages
These mechanisms benefit both parties. Clients gain earlier use of completed areas, while contractors receive partial payments sooner.
RICS guidance notes recommend using NEC’s sectional completion approach for complex developments with multiple stakeholders or end-users. The contract requires precise definition of section boundaries to prevent disputes.
Quality management remains consistent across sections through unified inspection procedures maintained in the works information.
Achieving Practical Completion and Addressing Latent Defects
Practical completion under NEC contracts applies the ‘completion for all practical purposes’ standard. This acknowledges the impossibility of perfection while requiring substantive compliance with contractual requirements.
The NEC engineering and construction contract distinguishes between:
- Patent defects (visible at completion)
- Latent defects (hidden at completion)
Contractors must remedy all patent defects before receiving the completion certificate. The de minimis principle applies, allowing minor imperfections that don’t affect functionality.
For latent defects, NEC establishes a defects date (typically 52 weeks after completion) during which the contractor remains responsible for remedying issues. Professional competence standards determine whether defects existed at completion but were hidden.
The Project Manager must fairly assess completion, balancing client expectations against reasonable construction standards.
Why NEC?
Enhanced Project Management: NEC contracts promote best project management practices, ensuring projects are completed on time and within budget.
Collaborative Approach: Designed to prevent costly disputes and replace traditional adversarial contracts, NEC fosters collaboration among project stakeholders.
Government & Industry Endorsements: Trusted by governments and industry bodies, NEC contracts have a proven track record of successfully delivering large-scale projects.
Core Features of NEC Contracts:
Core Clauses & Main Option Clauses: Providing a solid foundation and flexibility for different project needs.
Early Warning & Compensation Events: Emphasising proactive management of unforeseen circumstances.
Dispute Resolution: Clear mechanisms for efficient and fair conflict resolution.
Disallowed Costs: Transparent guidelines to ensure financial fairness.
NEC4 Updates: Latest improvements to tackle contemporary project management challenges.
Why Quantity Surveyors Need NEC Knowledge:
Essential Expertise: Understanding NEC contracts is crucial for Quantity Surveyors to manage costs, timelines, and resources effectively.
Proactive Risk Mitigation: Knowledge of NEC helps Quantity Surveyors identify and mitigate potential risks, ensuring smooth project progression.
Financial Mastery: NEC’s clear guidelines on reimbursable and disallowed costs enable Quantity Surveyors to maintain precise financial control over projects.
Conflict Resolution: Familiarity with NEC’s dispute resolution mechanisms empowers Quantity Surveyors to prevent and resolve conflicts efficiently, safeguarding project success.
NEC contracts have revolutionised the infrastructure and construction industry by replacing traditional adversarial contracts with a more collaborative and efficient approach. They continue to set the standard for successful project management and delivery in the construction sector.
Looking for a Career Change?
Check out our latest Job Listings