Building Construction Programmes from First Principles: A Comprehensive Guide to Foundational Approaches
Building construction programmes form the backbone of successful projects, guiding teams from initial concept to final completion. When created from first principles, these programmes offer a logical, structured approach that considers every aspect of the construction process. They break down complex projects into manageable components, allowing for better planning and execution.
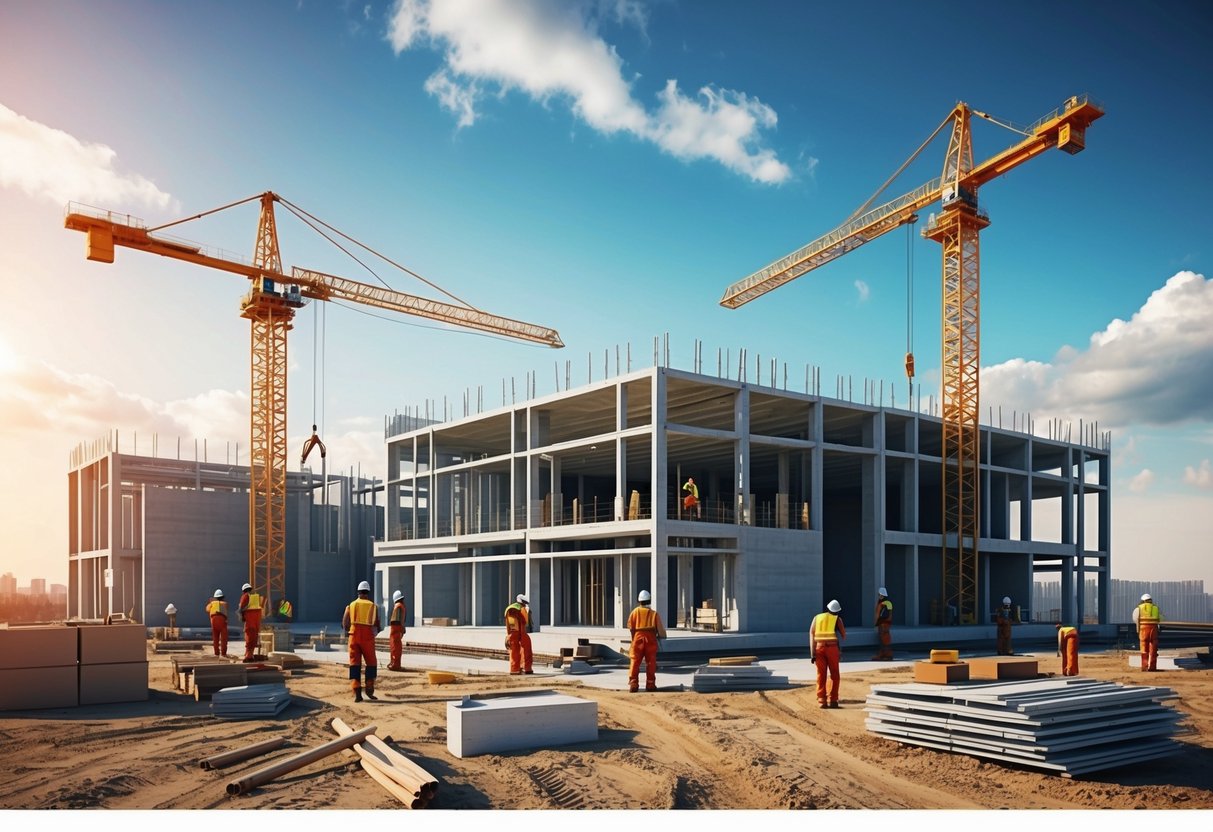
Effective construction programmes built from first principles help teams understand what resources they need, how much the project will cost, and how long it will take to complete. This approach involves calculating the monetary rates, labour hours, and productivity rates for each individual task rather than relying on historical data alone. The result is a more accurate timeline and budget that accounts for the unique aspects of each project.
Creating a well-structured Work Breakdown Structure (WBS) is essential to this process. Construction teams can organise their programme based on geographical areas or by the final structures and products needed for the main works. This systematic approach helps identify potential issues early, reduces costly mistakes, and ensures all stakeholders understand their responsibilities throughout the project lifecycle.
Fundamentals of Building Construction
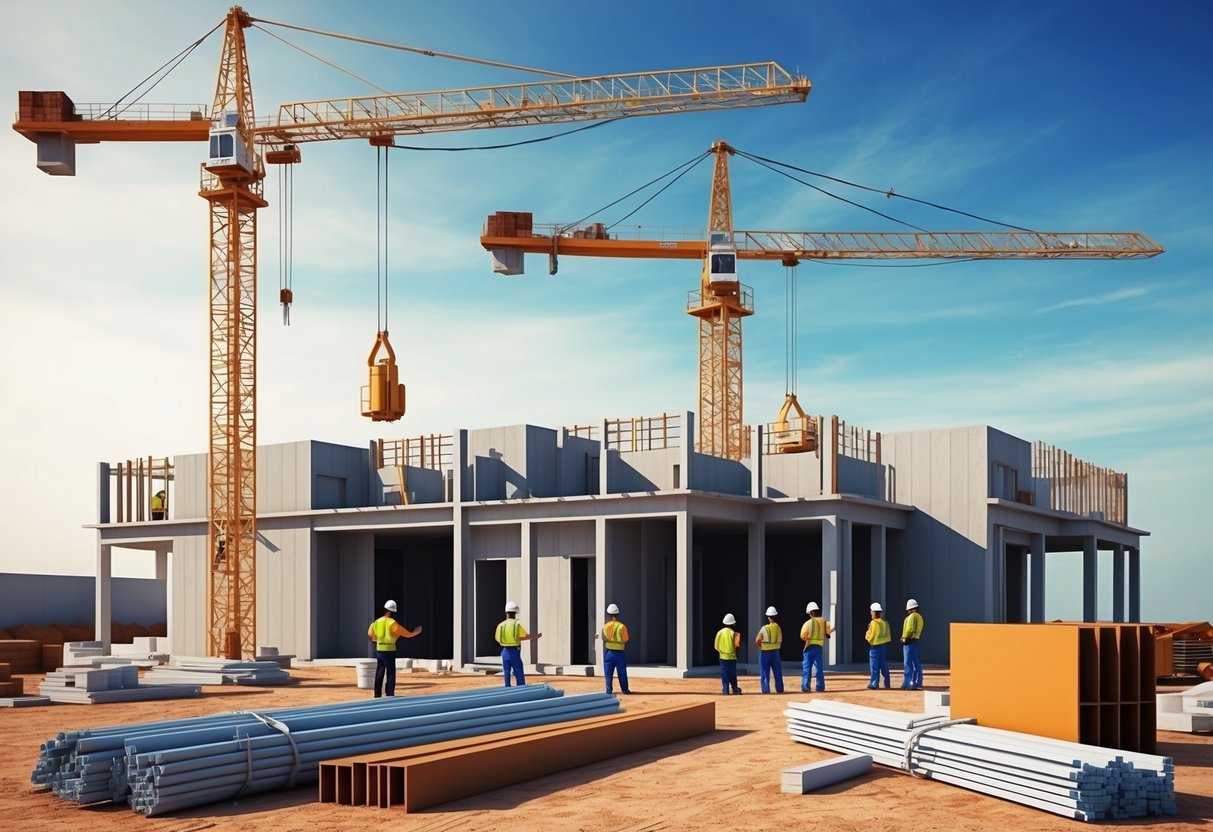
Building construction relies on several interconnected principles that form the foundation of any successful project. These fundamentals ensure structures are safe, functional, and durable when properly implemented.
Construction Materials and Properties
The selection of appropriate materials is crucial in building construction. Common materials include concrete, steel, timber, masonry, and glass, each with distinct properties and applications.
Concrete offers excellent compressive strength and durability, making it ideal for foundations and structural elements. It can be reinforced with steel to overcome its poor tensile strength. The water-cement ratio significantly affects concrete’s final strength and workability.
Timber provides good strength-to-weight ratio and natural insulation. It comes in various forms including dimensional lumber, engineered wood products (like glulam and CLT), and sheet materials. The moisture content of timber must be controlled to prevent warping or shrinkage.
Steel delivers exceptional tensile strength and ductility. Structural steel is categorised by its yield strength and comes in standardised sections such as I-beams, channels, and angles. Steel must be protected from corrosion through galvanising or coating systems.
Structural Design Principles
Structural design ensures buildings can safely withstand applied loads while maintaining stability. Engineers consider dead loads (permanent weight), live loads (occupants/furnishings), and environmental loads (wind/snow).
The principle of load paths tracks how forces transfer through a structure to the foundation. Every element must effectively transmit these forces to maintain structural integrity.
Primary Structural Systems:
- Frame structures (columns and beams)
- Load-bearing wall systems
- Shell and spatial structures
- Tensile structures
Factor of safety calculations prevent failure by designing structures to withstand loads greater than expected maximum loads. This accounts for material variations, construction tolerances, and unforeseen conditions.
Building connections deserve special attention as they often represent potential failure points. Bolted, welded, and nailed connections must be properly designed and executed.
Building Codes and Regulations
Building regulations establish minimum standards for safety, health, welfare, and accessibility. In the UK, the Building Regulations 2010 and associated Approved Documents provide the regulatory framework.
Key regulatory areas include:
- Structural safety (Part A)
- Fire safety (Part B)
- Site preparation and resistance to contaminants (Part C)
- Thermal performance and energy efficiency (Part L)
- Ventilation and indoor air quality (Part F)
Planning permissions must be obtained before construction begins on new buildings or significant alterations. This process ensures compliance with local development plans and considers environmental impact.
Inspections occur at critical stages of construction to verify compliance with approved plans and building regulations. Building Control Officers or Approved Inspectors typically conduct these inspections to ensure quality standards are met.
Planning and Project Management
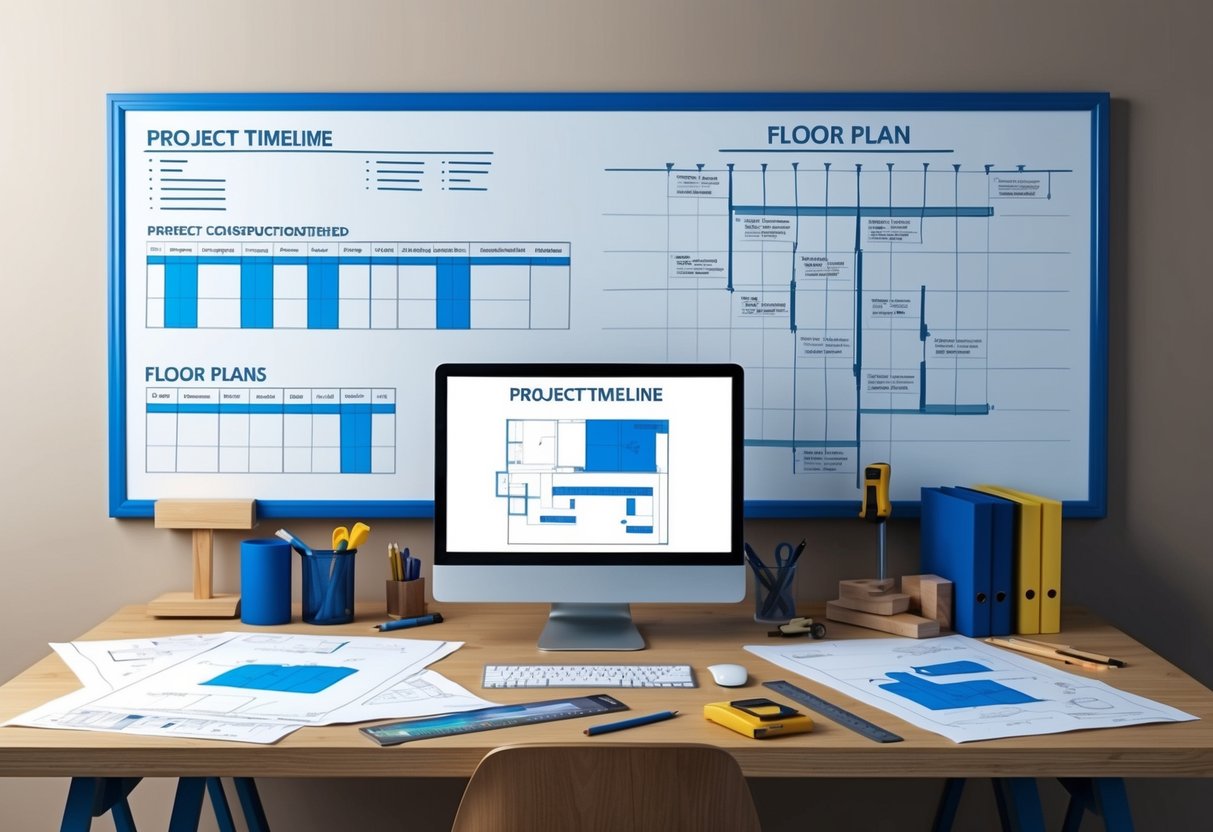
Effective planning and project management form the backbone of successful construction programmes. Every construction project requires careful coordination of activities, resources, and timelines to achieve desired outcomes within constraints.
Project Lifecycle Stages
Construction projects typically progress through five distinct stages. The initiation stage identifies project goals, feasibility, and stakeholder requirements. During this phase, project teams define what needs to be built and why.
The planning stage involves creating a Work Breakdown Structure (WBS) based on geographical areas or final structures, as noted in industry best practices. This stage produces detailed schedules, resource plans, and baseline budgets.
The execution stage is when physical construction begins. Project managers monitor progress against the plan, often using critical path method scheduling to track dependencies.
The monitoring and controlling stage runs concurrently with execution. Teams track performance metrics, manage changes, and implement corrective actions when needed.
The closing stage includes final inspections, handover procedures, and documentation of lessons learned for future projects.
Resource Allocation and Budgeting
Resource allocation involves identifying and assigning the necessary labour, materials, equipment, and subcontractors to project activities. Construction managers must balance resource availability with schedule requirements to prevent bottlenecks.
First Principles Estimating provides a reliable approach to budgeting. This method involves calculating costs by identifying individual quantities, production rates, and unit costs rather than relying on historical data alone.
Key components of construction budgeting:
- Direct costs (labour, materials, equipment)
- Indirect costs (supervision, site facilities)
- Allowances for risk and contingency
- Overhead and profit margins
Regular cost monitoring allows teams to identify variances early. Cash flow forecasting helps ensure adequate funding throughout the project lifecycle, preventing costly delays due to financial constraints.
Risk Management
Construction projects face numerous uncertainties that can impact schedules, costs, and quality. Effective risk management begins with systematic identification of potential threats and opportunities.
Risk assessment involves evaluating both the probability and potential impact of each identified risk. This analysis helps prioritise which risks require mitigation strategies.
Common construction risks include:
- Weather disruptions
- Supply chain delays
- Labour shortages
- Design changes
- Regulatory compliance issues
- Safety incidents
Mitigation strategies might include schedule buffers, alternative procurement routes, or contingency funds. The most effective approach is continuous risk monitoring throughout the project, with regular reviews and updates to the risk register.
Risk management should be proactive rather than reactive. Early identification allows for more cost-effective solutions before problems escalate into major issues affecting project success.
Construction Methods and Technologies
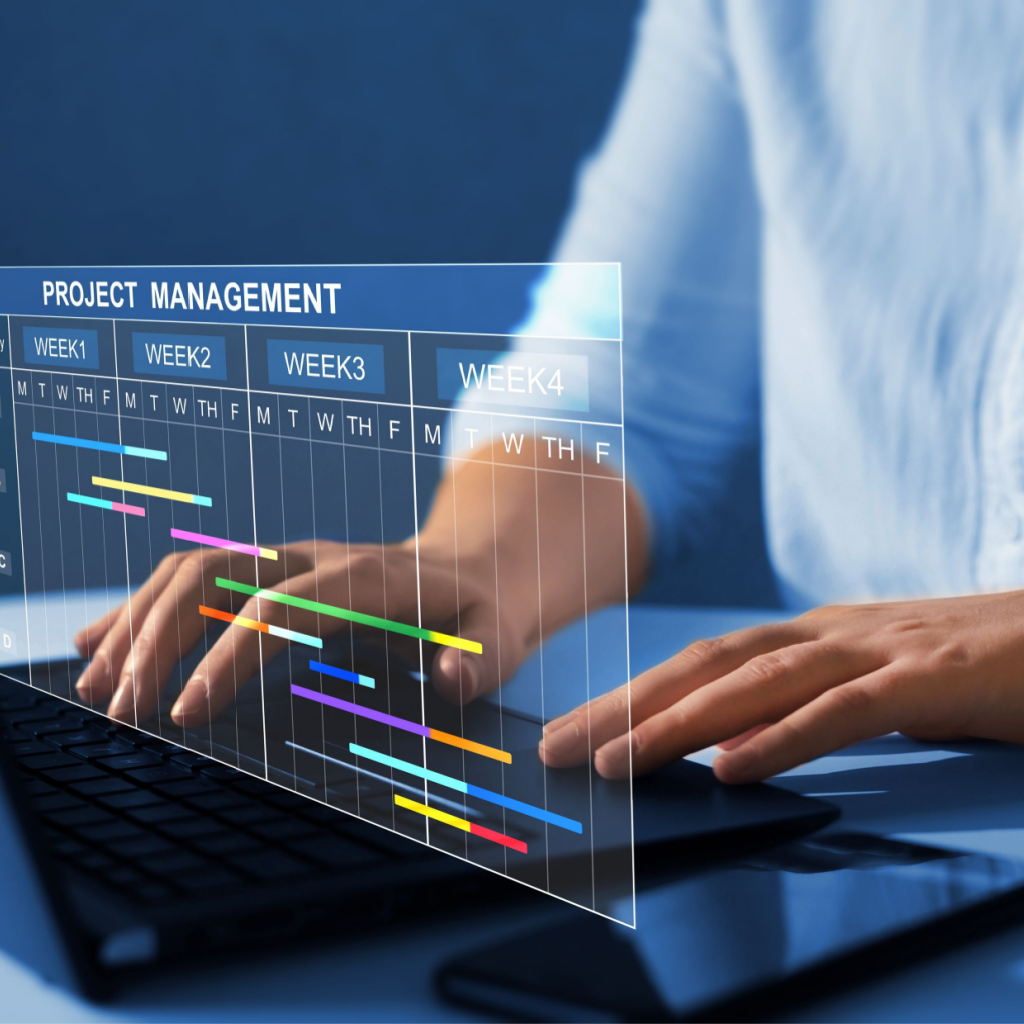
Construction methods have evolved significantly to meet modern demands for efficiency, cost-effectiveness and environmental responsibility. These advancements help builders create structures that are not only durable but also aligned with contemporary needs.
Modern Construction Techniques
AI-driven forecasting and IoT technologies now play crucial roles in construction planning and execution. These tools collect on-site data and provide dynamic insights that enable proactive decision-making throughout the building process.
Prefabrication has revolutionised construction by moving significant portions of building assembly to controlled factory environments. This approach reduces on-site construction time by up to 50% while improving quality control.
Building Information Modelling (BIM) allows teams to create detailed 3D models that simulate the entire construction process before breaking ground. This technology helps identify potential issues early, saving both time and resources.
Modular construction techniques have gained popularity for their efficiency and adaptability. These methods involve creating standardised components that can be assembled quickly on-site, particularly useful in housing and commercial projects.
Sustainability in Construction
Green building materials have become essential in modern construction programmes. Products like recycled steel, bamboo flooring and low-VOC paints reduce environmental impact while maintaining structural integrity.
Energy-efficient designs incorporate passive heating and cooling strategies to minimise resource consumption. Features such as proper orientation, thermal mass and natural ventilation can reduce energy needs by 30-50%.
Water conservation systems, including rainwater harvesting and greywater recycling, are increasingly integrated into building designs. These systems can reduce water usage by up to 40% in residential buildings.
Circular economy principles encourage reusing and recycling building materials throughout their lifecycle. This approach reduces waste and creates more sustainable construction practices for long-term environmental benefits.
Workforce Management and Safety
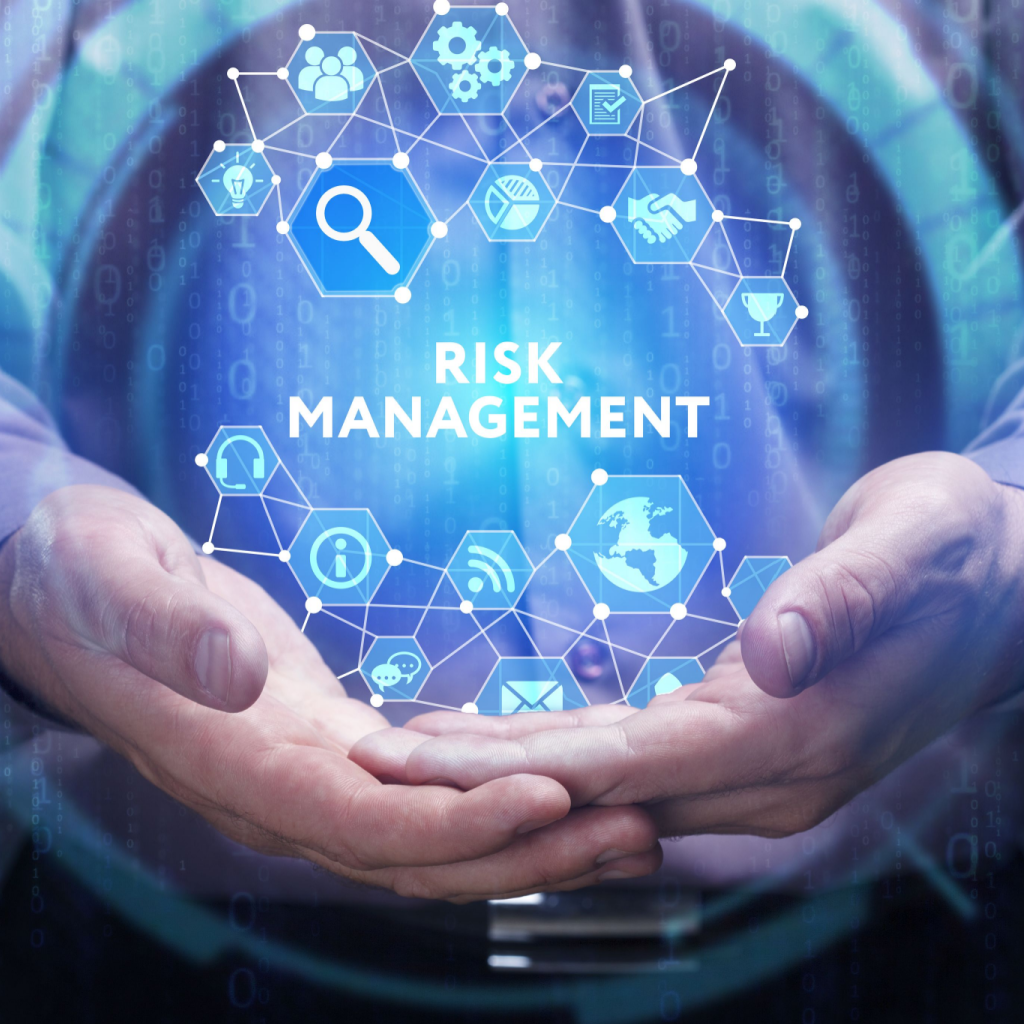
Effective workforce management and adherence to safety standards form the foundation of successful construction projects. These elements not only ensure regulatory compliance but also contribute significantly to project efficiency, timely completion, and the overall wellbeing of workers.
Labour Skills and Training
Construction projects require workers with specific skills and qualifications. Proper training programmes must be established early in the project planning phase to ensure all personnel meet the necessary competency levels.
Skills assessment helps identify gaps in the workforce capabilities. Project managers should maintain a skills matrix documenting each worker’s qualifications, certifications and experience. This approach enables strategic assignment of tasks based on individual capabilities.
Training should cover both technical skills and site-specific protocols. This includes equipment operation, material handling procedures and quality control processes. Regular refresher courses help maintain standards throughout the project lifecycle.
On larger projects, specialist roles must be clearly defined with appropriate certifications verified. Apprenticeship programmes can be integrated to develop skills while meeting labour needs.
Health and Safety Standards
Health and safety compliance is not merely a legal obligation but a fundamental principle of ethical construction management. The principal contractor assumes responsibility for establishing and enforcing safety protocols during the construction phase.
A comprehensive risk assessment should identify potential hazards before work begins. This assessment forms the basis for developing safety procedures tailored to specific project conditions. Regular safety audits must be conducted to ensure ongoing compliance.
Personal protective equipment (PPE) requirements should be clearly communicated and enforced. This includes:
- Hard hats and safety footwear
- High-visibility clothing
- Respiratory protection where necessary
- Fall protection systems for elevated work
Safety training must be provided to all workers before they begin on-site activities. This should cover emergency procedures, accident reporting protocols and specific site hazards. Documentation of this training is essential for regulatory compliance.
Regular toolbox talks help reinforce safety awareness and address emerging concerns. These brief meetings serve as reminders of best practices and provide opportunities for workers to voice safety observations.
Quality Assurance and Control
Quality assurance and control processes are vital for ensuring that construction projects meet standards, prevent defects, and deliver the expected value. These systematic approaches involve careful planning and rigorous testing throughout the project lifecycle.
Quality Planning and Procedures
Quality planning begins at the project’s inception with clear documentation of requirements and standards. A comprehensive Quality Management Plan (QMP) should outline specific objectives, responsibilities and required documentation for the project.
The QMP typically includes:
- Quality standards to be followed
- Roles and responsibilities of team members
- Control procedures for materials and workmanship
- Documentation requirements
Regular review meetings help keep quality objectives aligned with project progress. These sessions should involve key stakeholders to ensure everyone understands their quality responsibilities.
Construction Quality Assurance (QA) is proactive, focusing on preventing defects before they occur. This approach saves time and money by reducing rework and delays.
Testing and Inspection Protocols
Testing and inspection form the backbone of quality control in construction. These activities verify that work meets specifications and identify issues requiring correction.
Common inspection activities include:
- Material verification upon delivery
- Workmanship checks during construction
- Systems testing prior to handover
- Final inspections before completion
Inspection schedules should align with construction milestones, with critical elements receiving more frequent checks. Documentation of all inspections provides an audit trail and contributes to the project’s Health & Safety file.
Advanced testing methods may include non-destructive testing, performance testing and commissioning activities. These verify that systems function as designed before handover.
Testing protocols should be established early and communicated to all parties. This ensures everyone understands acceptance criteria and testing procedures.
We are often asked via our network for planning engineers that are able to build programmes from first principles We thought we would share this article written by a Senior Planning Engineer who was asked to illustrate this prior to attending an interview. Here is an example of one technique that can be used.
Write down the following from the contract document which should include :
- work information
- Access dates for parts of the site.
- Key dates in the contract and the conditions to be met for each key date i.e., the start and completion date.
- The sequence of works stipulated by the client.
- Requirements for health & safety set out in the Contract.
- Plant and material provided by the client and associated conditions thereof.
- Establishing the Work Breakdown Structure in a high level (WBS level 2), for example – Contract Data, Engineering (Design), Procurement, Main Physical Work, Assurance and Handing Over.
- For design work, the best bet is to create more WBS as appropriate, then build the programme considering the various design gate meetings. Creating milestones and linking them for the beginning of physical work at appropriate WBS would also be beneficial. Creating a separate WBS for the procurement of long lead and critical items would be helpful and useful.
- Start and complete your design for the WBS of the main physical works – based on geographical area or by final structure/product for main works. It would be good to take into consideration a combination of both since it will allow you to go deep into level 5 or 6. Definitely check this against the schedule of works given in the Contract. You’ll want to establish the relationship with the Activity Schedule & its cost as provided in the Contract.
- Look into the data source to ascertain the productivity if the contractor has not already provided this information for you. Once located use the information to figure out the duration for each of the activities identified. Meanwhile ascertaining the duration of activities, a special thought would be given to assign Time Risk Allowance, considering other risks associated with the activities.
- Reflect on the sequence as stipulated in the Contract and other contractual requirements. If needed the next thing to organise are workshops with pertinent team members to ascertain the relationship between activities. Once done you’ll also want to cover testing & commissioning activities and other assurance activities like Health & Safety file, As Built drawings, Engineering Safety Justification, Preparation of Snag list etc.
- If needed, iterations can be done until Contract requirements are met. Programme Integration Check is next – this is where you’ll be using Defence Contract Management Agency’s (DCMA) 14 rules or a similar integration test. Furthermore, you’ll need to establish the Critical Path of the programme.
- Once all 14 rules of DCMA completed and checked, make sure that all the Key Dates in the Contract Data have been reviewed and rechecked against the Contract. Once the Planned Completion Date and Terminal Float have been established you will load the Cost at WBS level 4 and reconcile with the Project Cost.
- Ask a member of the Risk Team to do a risk workshop and identify risks associated with the programmes. Identify the activities and its risks and keep a copy of this document. You could also identify the duration of each activity in terms of “Most Likely”, “Most Pessimistic” and “Most Optimistic”.
Infraspec serves as a specialist recruitment firm focusing on key roles in infrastructure projects. Our expertise centres on finding qualified professionals for planning, controls, cost management and risk assessment positions. Our company supports the construction industry by connecting talented individuals with organisations needing specialised skills for project delivery.
Working with various infrastructure projects, Infraspec helps address the critical need for proper planning and cost control—essential elements for successful project management. Our recruitment services support the construction planning process and help maintain effective supply chains through strategic staffing solutions.
We understand how infrastructure projects require specific expertise in risk assessment and controls, contributing to continuous improvement in the sector through better talent placement. Oheir services assist organisations in maintaining proper cost control and enhancing project management capabilities through qualified personnel.
Looking for a Career Change?
Check out our latest Job Listings